
In the 1870s, Europe’s industrial revolution was in full swing. Locomotives and factories were being powered by steam but small scale transport was increasingly being powered by the horse. Even a small city of 500,000 inhabitants might have 100,000 horses. Each horse would deposit up to 15kg of manure and 4 litres of urine on the city roads each day – it was the looming environmental crisis of the time. An affordable, reliable, small-scale engine that could replace the horse would be a godsend.
The steam-powered external combustion engine was one candidate: steam-powered cars were being developed. Another option was the internal combustion engine, early versions of which ran on petrol, gas, or even gunpowder. In an internal combustion engine, the fuel ignites inside a piston, does work, and then is expelled as waste gases.
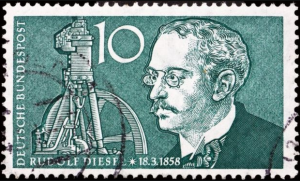
Into this world stepped a young German engineer named Rudolf Diesel. Born in France and raised in England, he later studied at the Industrial School of Augsburg in Germany. He then worked as an engineer and manager at a refrigeration and ice plant in Switzerland and became frustrated at the amount of energy wasted in steam driven industrial processes. Having an acute knowledge and understanding of thermodynamics, he set about designing an internal combustion engine. His work in engine design was driven by the goal of much higher efficiency ratios and in his engine, fuel was injected at the end of compression and the fuel was ignited by the high temperature resulting from compression. Today, this principle remains the fundamental difference between diesel and petrol powered engines. A further advantage of the diesel engine for the yacht owner is the relative safety of carrying large quantities of diesel oil as opposed to petrol; the flash point of diesel oil is considerably higher than that of petrol making it much less explosive.

Today’s modern diesel engines for road vehicles have almost universally adopted high-pressure common rial (HPCR) fuel injection systems. These systems have many advantages in terms of power output and operating efficiency but are extremely sensitive to contaminated fuel. Luckily, most boat owners still operate the generation of engines before this. This makes it easier for the part-time mechanic to maintain their own marine diesel engine.
The Four Stroke Diesel Engine
You probably know that your car engine is a four-stroke engine and your fifty-year old Seagull outboard is a two-stroke engine. Two-stroke petrol engines need oil added to their fuel and are often noisy and dirty. Curiously, the very, very large engines (like those producing over 100,000 hp for instance) that power tankers and cruise ships are also two-stroke engines although they run on heavy oil and rotate quite slowly. Most yacht auxiliary diesels, however, operate on a four-stroke cycle just like your car engine. On single cylinder engines (Yanmar 1GM / Volvo 2001 etc) this necessitates a large flywheel to keep the camshaft moving between power strokes. Let’s have a quick review of how these engines work. Remember this chestnut from school?
Suck. Squeeze. Bang. Blow.
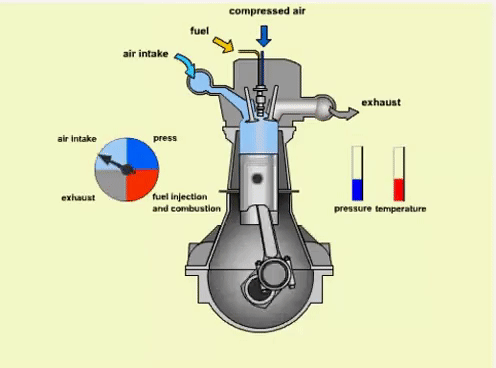
Stroke 1 – “Suck“
The intake stroke; the first stroke involves drawing clean air in to the cylinder. The piston moves from the top to the bottom of the cylinder. In this stroke the intake valve is open while the piston pulls air (without any fuel) into the cylinder by producing vacuum pressure into the cylinder through its downward motion.
Stroke 2 – “Squeeze“
The compression stroke; in the second stroke the piston moves from bottom of the cylinder to the top. In this stroke both the intake and exhaust valves are closed, resulting in compression of the air in the cylinder. During this compression the volume is reduced and thus the pressure and temperature both rise. At the end of this stroke fuel is injected and ignites in the compressed hot air. At the end of this stroke the crankshaft has completed a full 360 degree revolution from the beginning of stroke 1.
Stroke 3 – “Bang“
The power stroke; the piston moves from top to bottom. In this stroke both the intake and exhaust valves are closed. At the beginning of the power stroke, the ignited fuel burns which causes a rapid expansion in volume of hot gas in the cylinder, driving the piston down towards the crankshaft.
Stroke 4 – “Blow“
The exhaust stroke; the piston moves from bottom to the top during this final cycle. In this stroke the exhaust valve is open while the piston forces the exhaust gases out of the chamber. At the end of this stroke the crankshaft has completed a 720 degree revolution from the beginning of stroke 1. The system is now ready to repeat from stroke 1.
