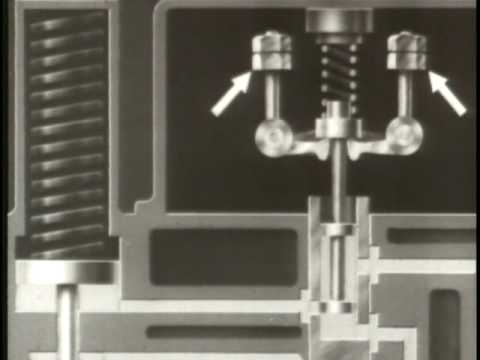

What does a Governor do in a Small Marine Diesel Engine?
All diesel engines with conventional mechanical fuel injection require some form of speed governor to control or limit the speed of the engine. To help control rotational speed when load fluctuates, Marine Diesel Engine have Governors.
The function of marine diesel engine governors is to control the rotational speed, or rev’s, of the engine as load fluctuates. It does this by regulating the amount of fuel which the injection pump can dliver to the injectors. Two-speed governors only exercise control of the idling and maximum (wide open throttle) speeds. Other govenors control fuel delivery (and thus, speed) throughout the entire range of the engineand are known as entire-range governors.
You may be more familiar with petrol engines – in gasoline or petrol engines the power output is controlled by the amount of air allowed to enter the carbuartor. A butterfly valve restricts the air inlet to the carburetor. As this valve opens, more air/fuel mixture is allowed into the cylinders and more power is delivered. A small marine diesel engine has no carburetor and no butterfly valve.
Air input is never deliberately restricted on a marine diesel engine. This is one reason why diesel engines are more efficient at low speeds and loads than gasoline alternatives. At low speeds, gasoline engines are throttling most of the air / fuel mixture which leads to extra load on the fuel pump, with subsequent pumping losses. And yes – that’s why it’s called a throttle!
The power output of a diesel engine is solely controlled by regulating the amount of fuel injected into the cylinders. Air intake is always about the same for each inlet stroke, regardless of engine speed, power output or load. At low speeds, very little fuel is injected and the available oxygen is only partially used. As the speed and load increase, more of this oxygen is burned until at full load, all of the available oxygen is being burned. To prevent posinous gases being exhausted, though, fuel injection is limited to about 75% of full combustion.
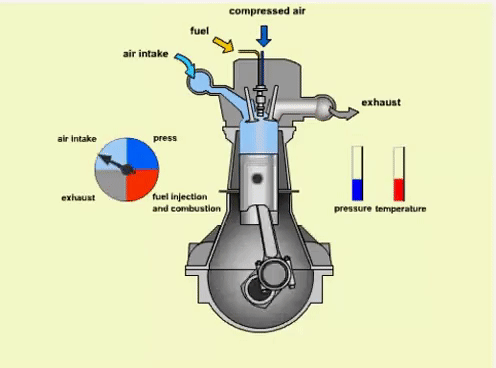
In most stationary engines, such as the industrial engines that our small marine diesels are modified from, we norally want to set engine rotational speed regardless of load variation. We really don’t want our engine labouring and racing as we plough through waves, for example. Constant rotational speed is achieved, therefore, by connecting the fuel-control lever on the injection pump to a governor device.
3 Main types of Marine Diesel Engine Governors
Type 1 – Flyweight or Centrifugal Governors
With development over generations, the broad category of centrifugal governors can be further divided down to exact types such as Porter, Proell, Hartnell, Wilson, Hartung, Pickering and, of course, Watt. Most small marine diesels employ a spring-loaded design which works well at sea.
In essence, a centrifugal governor consists of two weights, known as flyweights, each mounted on a hinged, spring-loaded arm. The governor’s driveshaft is directly driven by the engine and, as it spins, the flyweights spin out and lift up under centrifugal action. A speeder spring is often used to counteract the centrifugal force.
When the engine is running and load is constant, the flyweights (or flyballs) are in vertical equilibrium. Imagine the boat begins to climb up a wave; the load on the engine will now increase. The engine will begin to slow down, which will lower the flyweights. This action opens the throttle valve which allows more fuel through to the injectors. The engine will now induce more power and climb back up to its previous speed. When the load is reduced, the opposite happens.
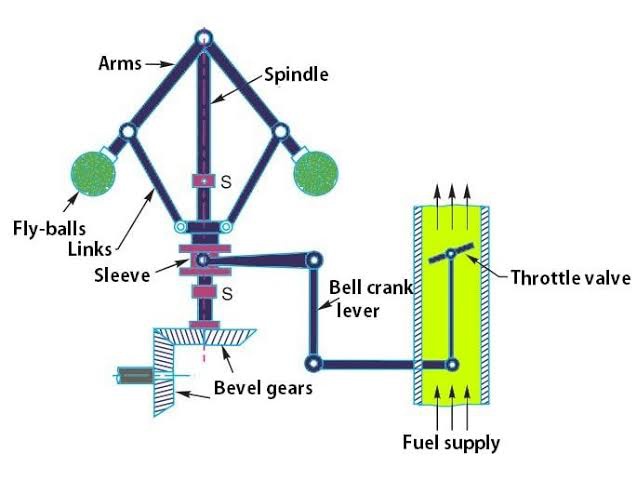
The Yanmar GM series engines employ a flyweight governor system.
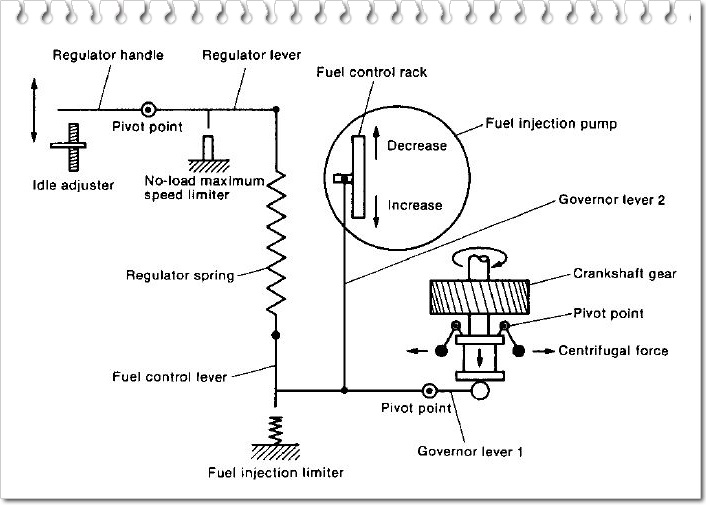
Fault Finding? Problems with mechanical flyweight governors generally fall under one of two categories – Damage to the Governor Spring or Sticking of the Governor Sleeve. Less common is damage to the bearings in the governor.
Type 2 – Hydraulic Type Governors
In very large ship engines, a centrifugal governer that directly controls fuel flow can be subjected to large forces and become inefficient. A similar but more complicated solution is to use hydraulic fliud to multiply the control forces.
In hydraulic governors, the centrifugal weights are connected to a control valve, rather than the fuel control racks directly. The control valve is responsible for directing hydraulic fluid which in turn controls the fuel racks and thus the power or speed of the engine. A greater force can be generated and larger fuel supply systems can be controlled. Most modern large ships use hydraulic governors with electronic control systems on top.
Yanmar produce the NZ range of hyraulic governers for use in very large marine diesel enigines.
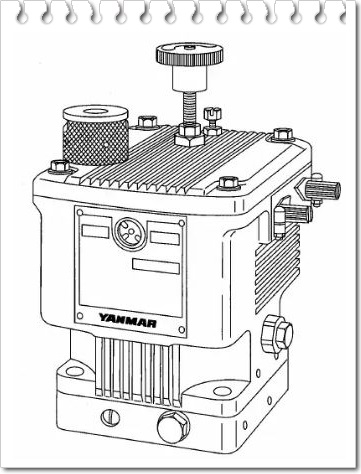
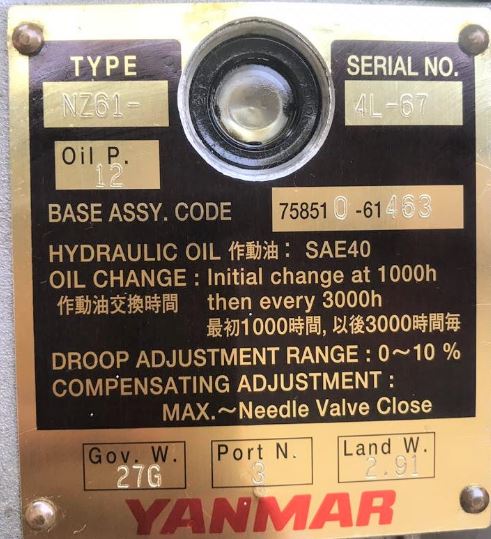
Type 3 – Electronic Type Governors
Common in modern automobile diesel engines, electronic governors use the engine’s built-in tachometer sensor to monitor the rpm of the engine. The sensor continuously feeds information back to the ECM (electronic control module). The ECM then computes all the information sent from all other engine sensors, such as the throttle position sensor, turbocharger-boost sensor, engine oil pressure and temperature sensor, engine coolant sensor, and fuel temperature to limit engine speed.
