
How do sacrificial anodes work?
When two dissimilar metals are in contact (electrically connected), and immersed in an electrolyte (such as salt water) they produce a galvanic cell (like a battery). As current (that is, electrons) flows from one metal to the other, the metal donating the electrons chemically changes form and corrodes. This process is called galvanic corrosion and will quickly destroy underwater metals. The way we counteract galvanic corrosion is to introduce a third metal into the circuit, one that is less noble than the other two to give up its electrons instead. This piece of metal is called a sacrificial anode, and in marine engine installations it is often made from zinc.
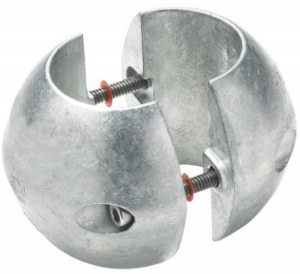
You will, no doubt, be familiar with the shaft anode shown above. The stainless steel of the shaft will cause the bronze of the propeller to corrode, and so we install a zinc sacrificial anode to prevent this happening. Metals can be placed on a scale – the galvanic scale – to let us know which will sacrifice themselves in any given pair. If two metals are in contact in an electrolyte (such as salt water) then the metal which is higher up the Galvanic Scale will corrode. You will notice that Zinc is second from top.

Heat exchangers in marine diesel engines are typically fabricated from a mix of copper alloy and mild steel. The steel is therefore at risk of galvanic corrosion. [Click here to read about particular Volvo Penta issues]. To combat this, many heat exchangers are fitted with a zinc “pencil” anode. You will find it usually under a plug or plate within in the exchanger. The pencil is unscrewed from the plug for replacement.

Raw water cooled engines have a similar zinc anode inside the cooling-water jacket to protect dissimilar metals in the engine. Determine if your engine and heat exchanger are fitted with internal anodes, and if so, check them at least annually. If they are any more than half depleted then replace them.

